Sensor Technology
Defined as 'devices that receive stimuli and respond with electrical signals', sensors are one of the most essential pillars of any intelligent electronics system. They form an interface between the physical world, determined by the laws of physics, and the digital world, which interprets the information provided for use in a wide range of applications.
Nowadays, sensor technology appears in new application fields and mass markets such as automotive, smart city infrastructures, and industrial automation & control. These areas use large arrays of sensors for collecting data that serve as inputs to the main control system, enabling intelligent decision-making.
The growth of smart phones and the IoT has spawned the development of many more types of sensors, especially the highly integrated, intelligent, low-power sensors. A few are designed to sense physical properties and others detect motion or proximity (using optical & light) and flow among others. Various technologies are used to achieve these objectives, including inductive, magneto-resistive, ultrasonic, optical, pressure, and capacitive.
Read more最新情報を入手
最新の情報や特別なオファーについてのお知らせをお送りいたします。
今すぐ購読
ご購読いただきありがとうございます
お申込みが完了いたしました製品、テクノロジー、アプリケーションに関する最新情報をお届けいたします。
Building blocks of Sensor Technology
Roll over the icons below for more information
Types of Sensing
Sensor IC
Optical & Light Sensors
Motion & Position Sensors
Flow Sensors
Sensing Transducers
Sensor Development Boards
Sensor Connectivity
Sensor Accessories
Temperature, Thermal Imaging & Test Equipment
Temperature, Thermal Imaging & Test Equipment
Transducers
Transducers are devices that convert any non-electrical quantity into a proportional electrical signal in the form of voltage or current. This can then be measured as a displacement, temperature, pressure, strain, or other physical parameter. Both actuators and sensors are forms of transducers, and any transducer in operation is functioning as either a sensor or an actuator at any given moment.
There are different types of transducers that are available in market. A few of them are temperature, pressure, displacement, inductive, resistive, capacitive, Hall Effect type, level, flow, force, and many more. Static response, dynamic response, environmental factors and reliability are just a few of the important parameters to be considered when selecting a transducer.
Strain gauges are often used in types of transducers where the corresponding output within the transducer design relates to the parameter being measured. Strain gauges are often used to determine the force as measured by a load cell, with the most popular being made of a semiconductor or a metal foil. Metal foil devices are generally crafted from copper-nickel alloy or nickel-chrome foils in a grid pattern arrangement, and utilise the resistance change that results from the deformation of the foil elements.
LVDTs and RVDTs (Linear and Rotary Variable Differential Transistors) are often used in conjunction with load cells and test systems to measure linear and rotational displacements. LVDT is a common type of electromechanical transducer that can convert the rectilinear motion of an object into a corresponding electrical signal.
Semiconductor devices use silicon or germanium strain gauges and the piezo resistive properties of these materials. Piezoelectric transducers have been widely used for sensing and actuation applications. When a piezoelectric material is squeezed or stretched, an electric charge is generated across the material, which is called 'direct piezoelectricity'.
A pressure transducer converts pressure to a digital or analog signal. Multiple technologies can be used to reach this objective, although a strain gauge is the preferred technology for such critical applications. When a pressure transducer is exposed to a pressure it provides an output voltage proportional to this pressure. The voltage output must be calibrated to reflect the pressure level.
Motion
Motion sensors detect the movement of an object and can be used to trigger an action by determining the absence or presence of a target. They play an increasing role in our day to day activities.
An accelerometer is probably the most well-known motion sensor and is an electromechanical device that will measure acceleration forces. These forces may be static, like the constant force of gravity pulling at your feet, or they could be dynamic which is caused by moving or vibrating the accelerometer. Some accelerometers use the piezoelectric effect in which they contain microscopic crystal structures that get stressed by accelerative forces, which in turn causes a voltage to be generated. Another way to do this is by sensing changes in capacitance. If you have two microstructures next to each other, they have a certain capacitance between them. If an accelerative force moves one of the structures, then the capacitance will change. Add some circuitry to convert from capacitance to voltage and you have an accelerometer.
Passive infrared (PIR) sensors and reflective infrared sensors are also common types of motion sensors. PIR sensors can be designed to cover a wide sensing area, as they can detect the presence of a warm object. This type of sensor, rather than emitting light, detects the amount of change in infrared rays that occur when an object whose temperature is different from the surroundings moves. Reflective infrared sensors emit infrared rays from an LED and then detect the reflected rays to determine the distance to an object.
Position
Position sensors provide positional feedback and are able to offer precise motion control, counting and encoding functionalities to many systems. They can detect a target object, a person, a substance or the disturbance of a magnetic or an electrical field and convert this into an electrical output to take further action.
There are various types of position sensors based upon many differing sensing technologies, each having their own benefits or limitations. There are contact device types, such as limit switches, resistive position transducers, and non-contact device types, which includes magnetic sensors (hall-effect and magneto-resistive sensor), ultrasonic sensors, proximity sensors, and photoelectric sensors.
Gyroscopes (gyro sensors) are devices that use the Earth’s gravitational pull to help determine orientation. Their design consists of a freely rotating disk called a rotor, mounted onto a spinning axis in the centre of a larger and more stable wheel. As the axis turns, the rotor remains stationary to indicate the central gravitational pull, determining which way is down. The gyroscope maintains its level of effectiveness by being able to measure the rate of rotation around a particular axis.
Position measurement is frequently required in feedback loops for positioning control as they can measure the distance travelled by any device, starting from the device's reference position to a new position, by angular movement and rotation. The technologies for position sensing include Hall Effect, resistive, and magneto resistive.
As sensing technology improves, positioning devices continue to get smaller and better, opening the way for more applications than ever before. A key step in selecting a suitable position sensor is understanding the requirements of sensor size, measurement range, linearity, resolution, accuracy, repeatability, mounting constraints and environmental ruggedness.
Proximity
Proximity sensors are discrete sensors that sense when an object has come near to the sensor face. They are able to detect the presence of nearby objects without any physical contact. A proximity sensor emits a beam of electromagnetic radiation and looks for changes in the field or return signal. Proximity sensors are commonly used on Smartphones to detect accidental touch screen taps when held to the ear during a call. There are four fundamental types of proximity sensors - Inductive proximity sensor, capacitive proximity sensor, Ultrasonic proximity sensor and Photoelectric or Opto-electronic Sensors.
Inductive proximity sensors respond to ferrous and non - ferrous metal objects. They will also detect metal through a layer of non - metal material. Inductive proximity sensors consist of a coil wound around a soft iron core. The inductance of the sensor changes when a ferrous object is in its proximity. This change is converted to a voltage-triggered switch. Capacitive sensors respond to a change in the dielectric medium surrounding the active face without necessarily making physical contact and can thus be tuned to sense almost any substance. Capacitive sensors can also sense a substance through a layer of glass, plastic or thin carton.
Photoelectric sensors offer non-contact sensing of almost any substance or object up to a range of 10 meters. It consists of a light source (usually an LED, light emitting diode, in either infrared or visible light spectrum) and a detector (photodiode). Ultrasonic sensor utilises the reflection of high frequency (20 KHz) sound waves to detect parts or distances to the parts. Ultrasonic sensors are the best choice for transparent targets.
Current
A current sensor is a device that detects and converts current into an easily measurable output voltage, which is proportional to the current measured. There are a wide variety of sensors, each suitable for a specific current range and environmental condition. The selection of a current sensor depends on requirements for magnitude, bandwidth, accuracy, robustness, isolation, cost, size or cost. The value produced can be converted into a digital form for use by a control or monitoring system, or kept in analog and directly displayed by a current testing instrument.
A current sensing resistor is the most commonly used current sensor. It can be considered, a current-to-voltage converter, where inserting a resistor into the current path, the current is converted to voltage in a linear way. The technology used by the current sensor is important as different sensors can have different characteristics for a variety of applications.
Current sensors are based on either open or closed loop Hall Effect technology. A closed-loop sensor has a coil that is actively driven to produce a magnetic field that opposes the field produced by the current being sensed. The hall sensor is used as a null-detecting device where the output signal is proportional to the current being driven into the coil, which is proportional to the current being measured.
In an open loop current sensor, the magnetic flux created by the primary current is concentrated in a magnetic circuit and measured using a hall device. The output from the hall device is the signal conditioned to provide an exact (instantaneous) representation of the primary current.
Related product categories
Optical & Light
The light sensor is a passive device that converts the light energy into an electrical signal output. Light sensors are commonly known as Photoelectric Devices or Photo Sensors because they convert light energy (photons) into electronic signal (electrons). Phototransistors, photoresistors and photodiodes are some of the common types of light intensity sensors.
Photoelectric sensors use a beam of light to detect the presence or absence of an object. It emits a light beam (visible or infrared) from its light-emitting element. A reflective-type photoelectric sensor is used to detect the light beam reflected from the target. A beam of light is emitted from the light emitting element and is received by the light receiving element. Both the light emitting and light receiving elements are contained in a single housing. The sensor receives the light reflected from the target.
A phototransistor, on the other hand, uses the level of light it detects to determine how much current can pass through the circuit. So, if the sensor is in a dark room, it only lets a small amount of current to flow. If it detects a bright light, it lets a larger amount of current flow. A photoresistor is made of cadmium sulphide whose resistance is maximum when the sensor is in dark. When the photoresistor is exposed to light, its resistance drops in proportion to the intensity of light. When interfaced with a circuit and balanced with potentiometer, the change in light intensity will show up as change in voltage. These sensors are simple, reliable, and cheap, used widely for measuring light intensity.
In optic fibre sensor technology, instead of using air as the transmission medium the system uses fibre optic cable to transmit light between a source and a detector. Fiber optic sensors can be classified into two major classes: intrinsic sensors and extrinsic sensors. In intrinsic sensors, the fibre optic cable itself is the sensor, whereas in extrinsic sensors, the fibre optic cable is used to guide light to/from a conventional sensor.
Humidity
Humidity is the presence of water in the air. The amount of water vapour in the air can affect human comfort, as well as many manufacturing processes in a number of different industries. The presence of water vapour can also influence various physical, chemical, and biological processes.
Humidity sensors work by detecting changes that alter electrical currents or temperature in the air. There are three basic types of humidity sensors: capacitive, resistive and thermal. All three types will monitor miniscule changes in the atmosphere in order to calculate the humidity in the air.
A capacitive humidity sensor measures relative humidity by placing a thin strip of metal oxide between two electrodes. The metal oxide’s electrical capacity changes with the atmosphere’s relative humidity. Weather, commercial and industries are the major application areas.
Resistive humidity sensors utilize ions in salts to measure the electrical impedance of atoms. As humidity changes, so does the resistance of the electrodes on either side of the salt medium. Two thermal sensors conduct electricity based upon the humidity of the surrounding air. One sensor is encased in dry nitrogen while the other measures ambient air. The difference between the two measures the humidity.
Thermal humidity sensors conduct electricity according to the moisture in the surrounding air. To do so they compute deviation between thermal conductivity of humid air versus dry air.
Related product categories
Temperature
Temperature Sensors are devices that measure the amount of heat energy or coldness that is generated by an object or system. They allow the sensing or detecting of any physical change to that temperature and produce either an analogue or digital output.
A temperature sensor consists of two basic physical types: Contact temperature sensor types and Non-contact temperature sensor types. Contact types of temperature sensor are required to be in physical contact with the object being sensed and use conduction to monitor changes in temperature. Non-contact types of temperature sensors use convection and radiation to monitor changes in temperature.
A variety of devices are available to measure temperature, the most common of which are thermocouples, thermistors, resistance temperature detectors (RTD), and infrared types. Thermocouples are the most versatile, inexpensive, and have a wide range (up to 1200 degrees Celsius typically). These consist of two dissimilar metal wires joined at the ends to create the sensing junction. When used in conjunction with a reference junction, the temperature difference between the reference junction and the actual temperature shows up as a voltage potential.
Thermistors are semiconductor devices whose resistance changes as the temperature changes, however the relationship between the temperature and the resistance is nonlinear. They are good for very high sensitivity measurements in a limited range of up to 100 degrees Celsius.
Like sense element, RTDs also use precision wire, which is usually made of platinum. They use the phenomenon that the resistance of a metal changes with temperature, which makes them linear over a wider range, more stable and have better accuracy and resolution than thermocouples.
Infrared sensors use the radiation heat to detect the temperature from a distance. These noncontact sensors can also be used to sense a field of vision to generate a thermal map of a surface.
Related product categories
Pressure
A pressure sensor is a device, which senses pressure and converts it into an analog electric signal whose magnitude depends upon the pressure applied. Pressure is defined as force per unit area that a fluid exerts on its surrounding. Since they convert pressure into an electrical signal, they are also termed as pressure transducers.
Absolute pressure is measured relative to a perfect vacuum, atmospheric pressure is an example. A common unit of measurement is pounds per square inch absolute (psia). Differential pressure is the difference in pressure between two points of measurement. This is commonly measured in units of pounds per square inch differential (psid). Gauge pressure is measured relative to ambient pressure, blood pressure is one example. Common measurement units are pressure per square inch gauge (psig).
The SI unit for pressure is the Pascal (N/m2), but other common units of pressure include pounds per square inch (PSI), atmospheres (atm), bars, inches of mercury (in Hg), and millimetres of mercury (mm Hg).
Pressure sensors have been widely used in fields like automobile, manufacturing, aviation, bio medical measurements, air conditioning, hydraulic measurements etc. In automotive industry, pressure sensors form an integral part of the engine and its safety. In the engine these sensors monitor the oil and coolant pressure and regulate the power that the engine should deliver to achieve suitable speeds whenever accelerator is pressed or the brakes are applied to the car. In instruments like digital blood pressure monitors and ventilators, pressure sensors are needed for optimisation, as per the patient’s health and requirements.
Related product categories
Touch
A touch sensor is a type of device that captures and records physical touch or embrace on a device and/or object. It enables a device or object to detect touch or near proximity, typically by a human user or operator. Touch sensing input devices offer numerous possibilities for novel interaction techniques and it reliably replaces mechanical buttons and switches to eliminate mechanical wear and tear. These can be configured into simple sliders, rotary wheels, or touch pads for intuitive user interfaces.
A touch sensor primarily works when an object or individual gets in physical contact with it. Touch sensors are also known as tactile sensors and are sensitive to touch, force or pressure. It can be implemented using Capacitive or Resistive sensing technology.
Capacitive sensing is a technology based on capacitive coupling that can detect and measure anything that is conductive or has a dielectric difference from air. Capacitive touch screens distinguish and sense specific touch location-based on the electrical impulses in a human body, typically the fingertip. This enables capacitive touch screens to not require any actual force to be applied to the screen’s surface.
Capacitive touch screen technology is a popular and durable technology that is used in a wide range of applications. Capacitive touchscreens are very clear, offering up to 90% transparency. Due to its higher clarity than resistive technology it is used in smartphones.
Flow
A flow sensor (or meter) is a device that measures the rate of flow of a linear, nonlinear, mass, or volumetric fluid or gas. Flow sensors utilize both electrical and mechanical subsystems to measure changes in the fluid's physical attributes and calculate its flow. Flow sensors are applicable to gasses with operating temperature range of -20 °C to +400 °C, liquids with operating temperature range of -50°C to +180°C and can measure flow rates and direction from 0 m/s to 100 m/s. They are deployed to detect leaks, blockages, and pipe bursts. Measuring flow is important for the control of many types of equipment. These sensors are commonly used in medical devices, HVAC systems, Automobiles, chemical factories, industrial process and smart energy applications. The factors to be considered whilst selecting flow meters are the ease of calibration and maintenance, mean time between failure histories and spare parts availability at the specific plant site.
Flow sensors are selected based on the requirement specifications like flowrate information, whether continuous or totalized, and if the data is local or remote. If remotely, the transmission may be analog or digital. The evaluation of properties and flow characteristics of the process fluid factors are pressure, temperature, allowable pressure drop, density (or specific gravity), conductivity, viscosity and vapour pressure at maximum operating temperature are also important.
Flow sensors are classified into two groups: contact and non-contact flow sensors. If the liquid or gas being measured does not clog the pipe when it comes into contact with the sensor's moving parts, contact flow sensors are used. Non-contact flow sensors, on the other hand, have no moving parts and are commonly used for tracking liquids or gases. Similarly the kind of flow sensor can be either volume flow sensing or mass flow sensor systems. Gas flow sensors use a mass flow based system.
Related product categories
おすすめのコンテンツ
How-to
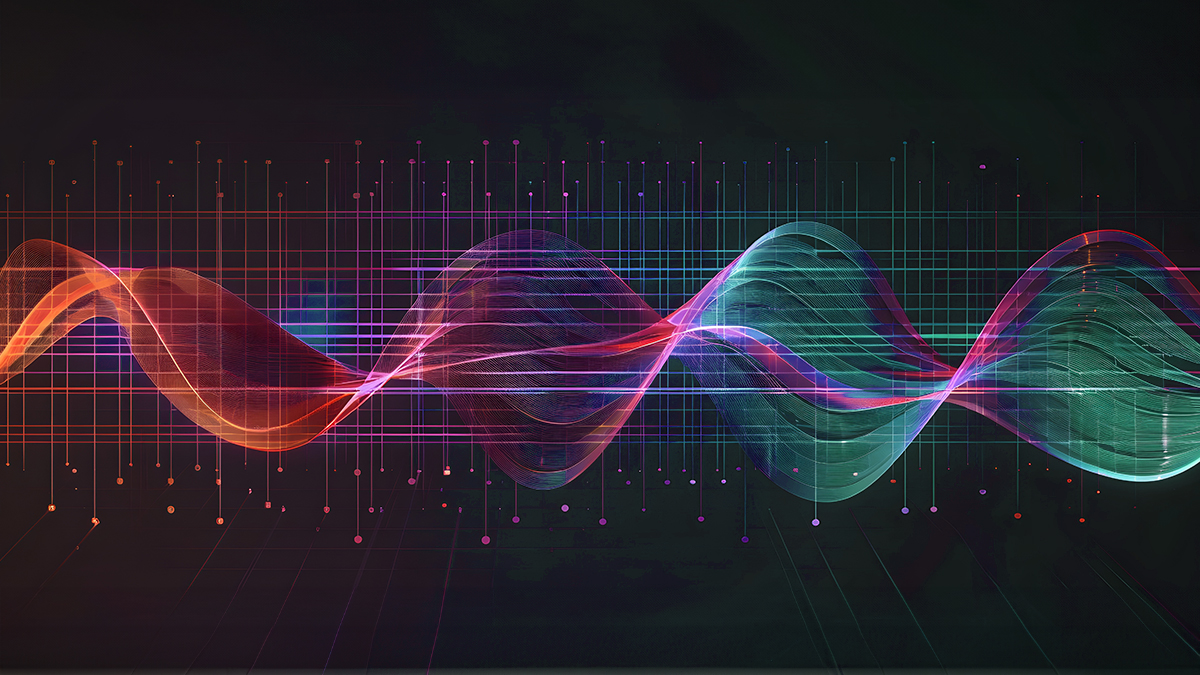
How to address EMI/RFI interference in capacitive touch sensing
Explore effective EMI management techniques, including shielding, grounding, and filtering, to enhance sensor reliability and signal quality in high-interference environments.
How-to

How To Optimize Low-Power Operation for Sensor Applications
Discover techniques to reduce sensor energy consumption without compromising functionality, crucial for wearable devices, remote monitoring, and IoT applications. Learn key factors to optimize low-power sensor operation.
Solution guide

Decoding Gas Sensors: Ultimate Guide to Cutting-Edge Gas Sensors Technologies
Discover how advanced gas-sensing technologies ensure industrial safety. Learn about different methods, their applications, pros and cons, and the importance of regular calibration for reliable detection.
Article

Sustainability and Sensors: Environmental Monitoring for a Greener Future
This article explains in detail the sensing solutions necessary for environmental monitoring by estimating the greenhouse gases in indoor environment, agricultural land and livestock farming for greener environment.